InFocus κ - Innovative thermophysical microscopy
Frequency-domain thermoreflectance microscope
Equipped with a galvano scanner capable of precisely scanning a diffraction-limited laser spot, our Laser Scanning FDTR Microscope enables groundbreaking 3-D nano-thermal analysis.
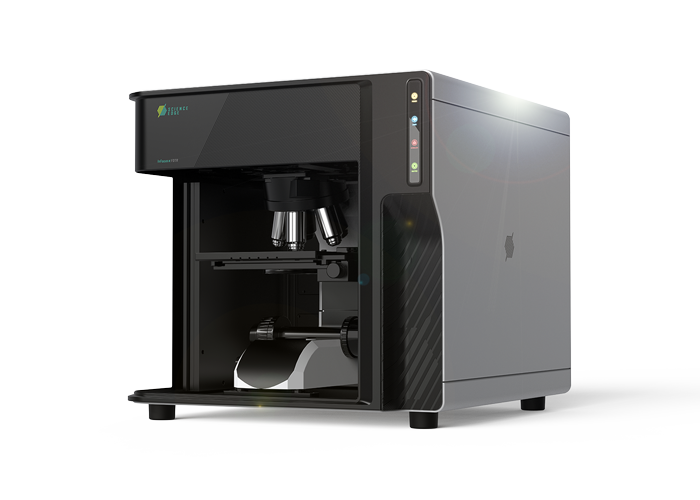
HIGHLIGHT
The diffraction-limited laser beam spot allows the evaluation of thermal properties of a small particle.
Evaluation of anisotropic thermal conductivity and thermal property microscopy are also available.
The temperature dependence of thermal conductivity can be evaluated using a cooling/heating stage (option).
- Overview
- Specifications
- Applications
- Papers
Overview
InFocus κ FDTR utilizes the phenomenon of thermoreflectance, where the reflectance of light on the surface of an object changes with temperature, to measure thermal properties such as thermal conductivity of thin films and microstructures and observe their distribution through Frequency Domain Thermoreflectance (FDTR) microscopy.
The key feature of InFocus κ FDTR lies in its ability to narrow down the laser beam spot size to near the diffraction limit and control its irradiation position freely through a laser scanning optical system. By utilizing a 3D thermal diffusion model in cylindrical coordinates for quantitative analysis, it enables evaluation of anisotropic thermal conductivity. Small laser spots also allow for evaluating thermal properties of single small particle such as heat dissipation fillers.
In addition, high-resolution Raman spectroscopy can be added as an option. Raman spectroscopy can provide additional information on a sample's molecular structure, crystallinity and residual stresses, facilitating multifaceted material analysis on a single instrument.
(Click "Introduction to frequency-domain thermoreflectance (FDTR)" for further information on FDTR.)
The sample surface is periodically heated at frequencies up to 50 MHz using a pump CW laser, and the phase delay of the temperature response is detected using a lock-in amplifier.
Evaluation of anisotropic thermal conductivity enabled by micro FDTR
InFocus κ FDTR can tightly focus the laser beam close to the diffraction limit. With a 20x (NA=0.45) objective lens, the 1/e2 beam diameters are 2.14 microns for pump beam and 1.19 microns for probe beam, and using 50x or 100x objective lens, the spot size can be narrowed down to submicron.
In measurements with Micro FDTR, thermal diffusion phenomena occur in three dimensions in many samples. Therefore, a three-dimensional thermal diffusion model using cylindrical coordinates is used for fitting analysis. If the sample has anistropic thermal conductivity, both the through-plane and in-plane thermal conductivities can be measured simultaneously by using them as fitting parameters.
It also features a function to calculate the measurement sensitivity of each fitting parameter, allowing for confident measurement by confirming the presence or absence of sensitivity beforehand.
Diverse measurement modes enabled by versatile scanning systems
One of the benefits of submicron beam diameter is the ability to measure the thermal conductivity of single small particle. Even micron-sized heat dissipating fillers can be measured by carefully focusing the laser on the centre of the particle.
In addition to scanning with an motorized stage, InFocus κ FDTR is equipped with a laser beam scanning system using a Galvanometer mirrors (probe light only). By combining a scan lens and a tube lens in an appropriate scanning optical system, the light is always irradiated perpendicular to the measurement plane, no matter where the beam irradiation position is.
In Beam Offset FDTR measurement, it is possible to measure the in-plane thermal conductivity sensitively by measuring while shifting the irradiation position of the probe light from the pump light. Furthermore, FDTR mapping measurement using stage scanning enables visualization of the distribution of various thermal properties.
Precise control of a laser spot using laser beam scanning technology
Using a laser scanning optical system, which is the specialized capability of ScienceEdge, the positions of the probe beam can be instantly changed by simply clicking anywhere on the software’s microscope image. The incident light on the sample surface is kept vertical; thus, spot-shape distortion will not be a cause for concern.
Specifications
Specifications
Model | InFocus κ FDTR |
---|---|
Pump laser | 445 nm Spot size: ~2 μm (@20x, NA=0.45) |
Probe laser | 514 nm Spot size: ~1 μm (@20x, NA=0.45) |
Transducer | Au |
Frequency modulation range | 10 kHz to 50 MHz |
Size | W505 × D560 × H480 mm |
Weight | 70 kg |
Others | Mapping function Anisotropic analysis High resolution Raman spectroscopy (Option) Cooling and heating stage (Option) |
*Product specifications are subject to change without notice. Please be aware of this in advance and check the details each time.
Image Gallery
Applications
Evaluation of anisotropic thermal conductivity in spin-chain–spin-ladder cuprates
Spin-chain–spin-ladder cuprates, as the name suggests, have a unique layered structure where ions are arranged in a ladder-like manner. Along the ladder legs (c-axis direction), it is known to exhibit high thermal conductivity due to magnons, whereas within the ab-plane, it shows low thermal conductivity due to phonons.
Here, we evaluated the thermal conductivity anisotropy of the single crystal La5Ca9Cu24O41 (LCCO), which exhibits the highest thermal conductivity at room temperature among spin-chain–spin-ladder cuprates, using InFocus κ FDTR.
Cr/Au was deposited by RF sputtering at a thickness of approximately 120 nm on the surface of a single-crystal LCCO that had been resin-embedded and polished with the ab surface exposed. We measured the phase delay of the thermoreflectance signal while varying the modulation frequency of the pump laser from 200 kHz to 10 MHz and conducted fitting analysis using a three-layer model in cylindrical coordinates (transducer/interface/LCCO).
The results of the fitting analysis show that the thermal conductivity in the through-plane direction (c-axis direction) is 45.3 W/mK and in-plane direction (ab-plane direction) is 5.1 W/mK. This through-plane thermal conductivity is consistent with the values reported in previous study*. Also, it is known that in LCCO, the in-plane thermal conductivity originating from phonons is about one-tenth of the through-plane thermal conductivity originating from magnons. This measurement also showed that the in-plane thermal conductivity approximately one-tenth of the through-plane direction, consistent with conventional understanding.
(Acknowledgments): We deeply appreciate Prof. Takayuki Kawamata from Tokyo Denki University for providing the single crystal LCCO and Prof. Nobuaki Terakado from Tohoku University for valuable advice on this measurement and data analysis.
*K. Naruse, et al. Solid State Commun. 154, 60–63 (2013).
Unit cell structure of LCCO. The ladder planes lie along the c-axis direction.(Reproduced with permission from H. Kinoshita, et al., npj 2D Mater. Appl. 6, 70 (2022).)
Phase data of single crystal LCCO measured with InFocus κ FDTR
Fitting analysis results (fitting parameters in green)
(Published Online: Apr. 9th, 2024)
Measuring thermal conductivity of single-crystal CVD diamond
Materials with extremely high thermal conductivity, such as diamond, pose a challenge to the quantitative evaluation of thermal conductivity. The difficulty arises from the difficulty of heating the sample sufficiently and from the minimal temperature response, including temperature relaxation and phase lag, making the measurement difficult.
Through a collaborative research effort with Associate Professor Jun Hirotani and Mr. Yuki Akura at Kyoto University*, ScienceEdge has developed an optical system capable of measuring even slight phase delays with high sensitivity. This advancement has made it possible to measure the thermal conductivity of materials with thermal conductivity exceeding 2,000 W/mK.
The graph on the right displays phase data measured with InFocus κ FDTR for a high-purity single-crystal CVD diamond substrate. By fitting with parameters such as interface thermal conductance between the transducer (Au/Cr) and diamond, and the thermal conductivity of diamond, the thermal conductivity of diamond was determined to be approximately 2,334 W/mK (see bottom right table).
*Note that part of this research was conducted under the support of the NEDO (New Energy and Industrial Technology Development Organization), as part of a project for discovering and supporting young researchers with challenges in startups, through a collaboration between the government and private sector.
Phase data of single-crystal CVD diamond measured with InFocus κ FDTR
Fitting analysis results (fitting parameters in green)
(Published Online: Feb. 28th, 2024)
Thermal conductivity measurement of amorphous Ge1-xSnx thin films using frequency-domain thermoreflectance
The thermal conductivities of amorphous Ge1-xSnx thin films with different Sn compositions were measured using InFocus κ FDTR. The results show that the thermal conductivity of the thin films decreases from 0.50 W/mK to 0.44 W/mK with increasing Sn composition, consistent with the amorphous limit calculated by the minimum thermal conductivity model.
(Published Online: Mar. 24th, 2023)
Papers
Yuki Akura, Yasuaki Ikeda, Yuki Matsunaga, Masaki Shimofuri, Amit Banerjee, Toshiyuki Tsuchiya & Jun Hirotani
“Frequency-domain thermoreflectance with beam offset without the spot distortion for accurate thermal conductivity measurement of anisotropic materials”
Rev. Sci. Instrum. 96, 014902 (2025)
Jun Hirotani, Taisuke Ota
“Measurement Error Reduction in Frequency-Domain Thermoreflectance Techniques”
The 69th JSAP spring meeting 2022, 22p-P03-23 (2022)